Kommissionierung
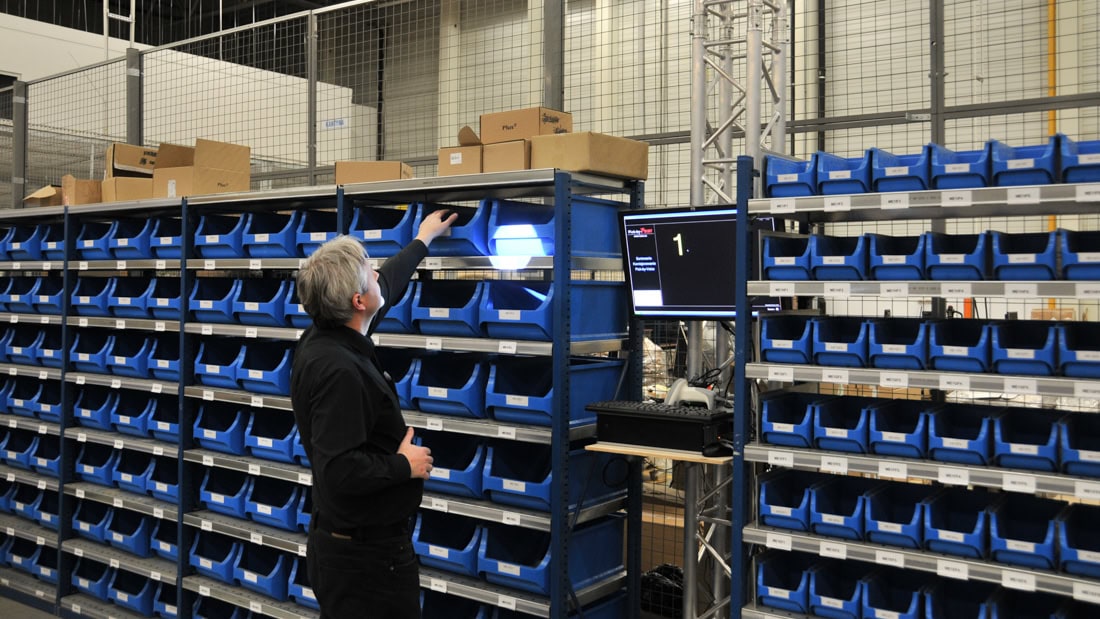
Die Ware aus einem Kommissionierlager, muss für die Auslieferung auftragsbezogen zusammengestellt werden. Diese Tätigkeit wird als Kommisionierung bezeichnet.
Was ist Kommissionierung?
Kommissionierung von Ware ist das Zusammenführen von Artikeln aus der Gesamtmenge zu einem Auftrag. Das Lagerverwaltungssystem steuert die Entnahmen aus den Lagerfächern mit diversen Kommissioniermethoden.
In dem Artikel finden Sie nicht nur die Definition oder Bedeutung von der Kommissionierung, sondern wichtige Informationen über die Kommissioniermethoden und Kommissionierzeiten.
Die Kommissionierung im Überblick
Das Zusammenführen von Aufträgen in einem Lager oder Produktion erfolgt manuell durch die Mitarbeiter (Kommissionierer / Picker) oder automatisch durch Kommissionierroboter und Maschinen. Der Unterschied kann grundsätzlich wie folgt bezeichnet werden:
- Mann-zu-Ware (manuell)
- Ware-zu-Mann (halbautomatisch)
- Vollautomatische Kommissionierung
Manuelle Kommissionierung
(Mann-zu-Ware)
In einem manuellen Prozess erfolgt die Zusammenstellung von Ware mit Hilfe von Picklisten oder verschiedenen Pick-Systemen. Die Arbeit mit Papier wird immer mehr durch beleglose Kommissionierung ersetzt. Die unterstützenden Systeme führen den Kommissionierer mit verschiedenen Kommissioniermethoden zu den passenden Lagerorten. Sie unterstützen ihn und kontrollieren bei der Entnahme der Ware.
Der Kommissionierer bewegt sich durch das Lager, um die Ware aus den Paletten, Durchlaufregalen, Fachbodenregalen etc. zu kommissionieren. Aus dem Grund wird die Methode Mann-zu-Ware bezeichnet.
Halbautomatische Kommissionierung
(Ware-zu-Mann)
Das Prinzip bei der halbautomatischen Kommissionierungsmethode ist umgekehrt. Die Ware wird in Ladungsträgern (Behälter oder sogar ganze Regale) aus dem Lager automatisch zu dem Kommissionierplatz transportiert und dem Kommissionierer im Zugriff bereitgestellt.
Der Kommissionierer bleibt also an seinem Arbeitsplatz und hat die Aufgabe, die Ware aus den Ladungsträgern in einer passenden Stückzahl zu entnehmen und an die Kundenaufträge zu verteilen. Aus dem Grund wird die halbautomatische Methode oft als Ware-zu-Mann bezeichnet.
Vollautomatische Kommissionierung
In einem vollautomatischen Kommissionierverfahren ersetzen die Kommissionierautomaten und Kommissionierroboter komplett den Mitarbeiter. Diese Kommissioniermethode ist jedoch nur für bestimmte Artikel geeignet, wobei nicht immer nur die Ware selbst, sondern auch die Wirtschaftlichkeit eine entscheidende Rolle bei der Auswahl der Kommissioniermethode spielt.
Oft sind die vollautomatischen Verfahren bei der Anschaffung und in den Betriebskosten zu teuer und haben einige Nachteile.
In diesem Artikel zeigen wir Ihnen mit welchen manuellen Kommissioniermethoden (Mann-zu-Ware) alles am besten funktioniert. Wir geben Ihnen nicht nur Tipps oder Definitionen dafür, sondern erklären ganz genau, warum eine beleglose Kommissionierung eindeutige Vorteile gegenüber der herkömmlichen Pickliste hat.
Die manuellen Kommissionierverfahren
Außer einer Pickliste stehen uns heute viele systemunterstützende Kommissionierverfahren zur Verfügung. Je nach Bedarf können verschiedene Systeme eingesetzt werden. Zu den besten und oft eingesetzten Kommissionierverfahren gehören:
- Pick-by-Scan
- Pick-by-Light
- Pick-by-Voice
- Pick-by-Point®
- Pick-by-Frame®
- Pick-by-Cart
- Pick-by-Watch®
- Pick-by-Tablet
Es gibt auch einige Erweiterungen und Sonderlösungen von LUCA Logistic Solutions:
- Pick-Radar®
- Pick-by-Weight
- Pick-by-RFID
- Pick-by-ePaper®
Alle Systeme von LUCA finden Sie in dem Menü „Systeme“ oder in der Liste an der rechten Seite oben. Alle diese Systeme werden von einem zentralen LUCA-Server verwaltet und können auch in der einstufigen Kommissionierung als Kombinationen eingesetzt werden. Wir sprechen in dem Fall von Hybrid-Lösungen. Mit all diesen Systemen können Kommissionieraufträge schneller, ohne gesonderte Einarbeitung, abgearbeitet werden.
Kommissionierzeiten
Um eine manuelle Kommissionierung effizient zu gestalten und den Kunden schnell zu beliefern, müssen in dem Prozess folgende Zeiten erfasst und optimiert werden.
Was ist eine Kommissionierzeit?
Die Kommissionierzeit ist eine Summe der einzelnen Zeiten, die für eine Kommissionierung benötigt werden:
Kommissionierzeit = Basiszeit + Wegzeit + Greifzeit + Nebenzeit (Totzeit) + Verteilzeit
Basiszeit
Die Basiszeit beinhaltet die organisatorischen Tätigkeiten vor und nach dem Kommissionier-Vorgang:
- Ausdruck der Picklisten aus der Lagerverwaltungssoftware (wenn nicht beleglos)
- Vorbereitung der Kartonagen, Behälter, Corletten oder Paletten
- Weitergabe der kommissionierten Aufträge
Wegzeit
Die Wegzeit definiert die Zeit für die Wegstrecke des Kommissionierers zwischen den einzelnen Lagerzonen und Lagerfächern. Diese Zeit kann einen sehr großen Einfluss auf die Gesamtleistung der Kommissionierung haben. Zu den wichtigsten Faktoren gehören:
- Größe der Kommissionierzonen und der Weg zu der nächsten Entnahme
- Orientierung im Lager, um das Lagerfach zu finden (Gasse, Regalreihe, Regalebene)
Hier soll auch immer die Möglichkeit der Multi-Order-Picking Methode untersucht werden.
Greifzeit
Ist der Kommissionierer an dem Regalfach angekommen, wird die Zeit für den Zugriff auf die Ware gemessen. Die Greifzeit wird auch als Entnahmezeit oder Pickzeit genannt. Hierzu zählen folgende Tätigkeiten:
- Zugriff auf die Artikel
- Abzählen der Mengen
- Ablage der Stückzahl in den Kommissionierbehälter
Die Optimierung der Greifzeit und der Fehlerquote hängt oft mit einer systemseitigen Unterstützung für das Zählen der Stückzahlen zusammen. Ansonsten ist die Greifzeit selbst nicht stark optimierungsfähig und hängt auch von der Art der Lagerung der Produkte ab (Palettenplätze, Durchlaufregale, Fachbodenregale, etc.).
Nebenzeit (auch Totzeit gennant)
Bevor der Kommissionierer auf die Ware zugreifen kann, erfolgen noch weitere Zusatztätigkeiten in der Bearbeitung, die dazu gerechnet werden müssen. Dazu gehören:
- Suchen der Lagerfächer
- Auf- und zumachen der Kartons oder Behälter im Lagerfach
- Steigen auf Leitern oder Benutzung von Hilfsmitteln
- Erfassung der Seriennummern, wenn erforderlich
- Sicherheitsverpackung der Artikel
- Entnahmequittierung
- Aufbringung von Beschriftungen und Etiketten
Die Nebenzeit (Totzeit) ist stark von den erforderlichen zusätzlichen Prozessschritten abhängig und kann durchaus auch gut optimiert werden. Die Zeit für Einarbeitung wird nicht berücksichtigt.
Verteilzeit
Zu der Verteilzeit gehören nicht produktive Tätigkeiten, die stark von der Mitarbeitermotivation und deren Einstellung zu der Arbeit abhängig ist. Dazu gehören:
- Pausenzeiten für persönliche Bedürfnisse (WC, Rauchen)
- Unnötige Gespräche mit den Arbeitskollegen (oft über private Themen)
- Warten auf nächste Vorgaben der Vorgesetzten
- Warten auf Reaktionen der Systeme (z.B. durch langsame Steuerungen und nicht optimale Abläufe)
Die Optimierung der Verteilzeit ist stark mit der Organisation, Motivation der Mitarbeiter und des Arbeitsklimas verbunden.
Kommissioniermethoden
In der Praxis geht es um die optimale Verteilung und Gestaltung der Auftragsdurchlaufzeiten, um einen Kundenauftrag schnell und kostengünstig zu kommissionieren. Aus dem Grund werden die organisatorischen Abläufe oft unterschiedlich gestaltet, um den Aufwand zu minimieren. Zu den grundlegenden Methoden gehören folgende Varianten der Kommissioniermethoden:
Auftragsorientierte, serielle Kommissionierung
Ein Kundenauftrag wird nacheinander in verschiedenen Lagerzonen durch einen oder mehrere Lagerarbeiter abgearbeitet. Diese Kommissioniermethode ist einfach und erfordert keine aufwändige Organisation. Die Einarbeitung und Definition der Verantwortungen für die Kommissionierer ist einfach. Nachteil der Methode sind lange Wegzeiten (lange Kommissionierwege) und die ungeregelte Übergabe der Aufträge in die nächste Kommissionierzone. Die gesamte Auftragsdurchlaufzeit ist nicht optimal.
Auftragsorientierte, parallele Kommissionierung
Jeder Auftrag wird in mehrere Teilaufträge getrennt, so dass das Zusammenführen der Artikel parallel erfolgen kann. Die Aufteilung der Aufträge in Teilaufträge kann nach verschiedenen Kriterien erfolgen, z.B. nach Lagerzonen, nach Artikelvolumen für den Transport, nach Verpackungskriterien, etc. Nach der Kommissionierung erfolgt dann die Zusammenführung der Teilaufträge.
Die Auftragsdurchlaufzeiten sind in der auftragsorientierten parallelen Kommissionierung deutlich kürzer als bei der auftragsorientierten, seriellen Kommissionierung. Der gesamte Materialfluss, die Organisation bei der Zusammenführung der Teilaufträge und die ungleichmäßige Auslastung der einzelnen Lagerzonen sind jedoch problematischer. Sie lassen sich mit einer entsprechenden Materialfluss-Steuerung und automatischer Fördertechnik jedoch gut regeln.
Serienorientierte, parallele Kommissionierung
Vor Beginn werden die Gesamtaufträge erst in Serien zusammengefasst und auf die einzelnen Lagerzonen parallel verteilt. Die Aufträge sollen aber nicht beliebig, sondern serienorientiert so zusammengefasst werden, dass pro Lagerplatz eine maximale Anzahl der Entnahmen erfolgen soll. Die Artikel werden erst gesammelt und dann auf die einzelnen Aufträge verteilt.
Vorteil dieser serienorientierten Kommissioniermethode ist, dass ein Lagerplatz nur einmal pro Serie und nicht pro Einzelauftrag angelaufen werden muss.
Lesen Sie noch mehr Details zu den einzelnen Kommissioniermethoden und erfahren Sie genau welche Kommissioniermethode, wann eingesetzt werden soll.
Das spart die Laufwege und verkürzt die Auftragsdurchlaufzeit. Die Verteilung der Artikel kann direkt bei der Entnahme mit Hilfe von Pick-by-Cart oder Pick-by-Frame® erfolgen. Die Alternative dazu ist eine spätere Verteilung an speziellen Arbeitsplätzen mit Put-to-Point® oder Put-to-Light. Die serienorientierte Kommissioniermethode erfordert eine ausgereifte technische Unterstützung.
Beispiel für den Ablauf einer einfachen Kommissionierung
Die Einzelaufträge werden in einem Lagerverwaltungssystem erfasst und daraus eventuelle Teilaufträge generiert. Das Zusammenstellen (Bereitstellen oder Zusammenführen) der Güter für die Verpackung oder Abgabe für die Produktion, nennt man dann Konsolidierung, die wir später noch in einem separaten Artikel genau beschreiben werden. Die Ablauforganisation kann hier sehr unterschiedlich sein.
In folgenden Punkten werden wir einen Kommissionierer mit einer Pickliste auf dem Papier und einen Kommissionierer mit einer beleglosen Kommissionierung direkt vergleichen und die Vor- und Nachteile in den einzelnen Schritten darstellen. Die Einarbeitung ist einfach.
Start der Aufträge
Bei einem Ablauf mit einer Kommissionierliste nimmt der Kommissionierer den nächsten gedruckten Auftrag mit und beginnt einfach seine Tätigkeit.
Die Aktivierung der beleglosen Kommissionieraufträge erfolgt mit unterschiedlichen Methoden, z.B. durch Einsatz von Barcode-Scannern (zum Beispiel: Lieferschein, Sammeleinheit, Behälter oder Karton), RFID oder durch Aktivierung der Aufträge auf einem MDE-Terminal. Die eingesetzte Technik hängt stark von dem gewünschten Prozess und Anzahl der Lagerzonen ab.
Nachteil einer beleghaften Kommissionierung bei dem Start ist, dass der Pickzettel verloren gehen kann, was zu einem kompletten Fehler in der Auftragsbearbeitung führen kann. Aus dem Grund werden hiefür spezielle Drucker für die Pickzettel aufgestellt, um einen eventuellen Verlust der Kommissionieraufträge durch unbeabsichtigte Mitnahme der Pickzettel zu vermeiden, was bei allgemein genutzten Druckern sehr schnell passieren würde.
Vorteil der beleglosen Kommissionierung ist hier, dass die Startzeit genau erfasst werden kann.
Führung zum Lagerplatz
Hat der Kommissionierer eine herkömmliche Pickliste in der Hand, muss er die nächste Lagerortbezeichnung ablesen, den Lagerplatz in der Lagerzone finden und optisch kontrollieren. Nachteil: Hier passieren oft nach vielen Stunden Arbeit Fehler, die zu schwerwiegenden Qualitätsverlusten führen.
Bei einer beleglosen Kommissionierung wird der Mitarbeiter visuell oder akustisch zu seinem Entnahmefach geführt. Für die Qualitätssicherung muss der Kommissionierer, je nach Kommissionierverfahren, den Lagerort durch Lesung des Barcodes oder per Sprache bestätigen. Zu den besten, schnellsten und sichersten Kommissioniermethoden gehören hier: Pick-by-Light, Pick-by-Voice, Pick-by-Frame, Pick-by-Point und Pick-by-Watch. Zu den schlechtesten Kommissionierverfahren in einem Lager gehören Anwendungen mit der Datenbrille: Pick-by-Vision.
Eindeutiger Vorteil gegenüber der Papierliste ist hier die Absicherung durch die Bestätigung des Lagerplatzes und die direkte Reaktion des Systems auf einen Fehler. Die hohe Kommissionierleistung ist durch die kurze Wegzeit (Suchzeit) gekennzeichnet.
Warenentnahme
Ist der Mitarbeiter mit der Pickliste bereits an dem richtigen Lagerfach angekommen, muss er die passende Textzeile wieder finden und die Stückzahl korrekt ablesen. Das Ablesen der Stückzahl gehört zu den größten Fehlerquellen bei der beleghaften Kommissionierung. Hier ist die Fähigkeit zur mehrstündigen Konzentration des Kommissioniers sehr gefragt.
Bei einer beleglosen Kommissionierung bekommt der Mitarbeiter die Menge direkt an dem Lagerplatz oder an seinem mobilen Gerät angezeigt. Bei dem sprachgeführten System wird die Stückzahl in dem Headset ausgegeben. Vorteil hier ist, dass der Mitarbeiter sich auf die Arbeit besser konzentrieren kann und das System ihn zu dem passenden Zeitpunkt über den nächsten Schritt informiert.
In beiden Fällen muss der Mitarbeiter die passende Menge selbst abzählen. Bei großen Stückzahlen empfehlen wir den Einsatz von Zählwaagen und einem Pick-by-Weight System.
Bestätigung der Menge
Die Entnahmemenge wird auf einer Kommissionierliste mit einem Kugelschreiber „abgehakt“ oder die Mindermenge notiert, die dann später in der Auftragsbearbeitung manuell nachgearbeitet werden muss.
Die Entnahmemenge wird in einem beleglosen System automatisch und sofort gebucht, was ein sehr großer Vorteil ist.
Abschluss
Sind alle Positionen auf einem Pickzettel erledigt, kann der Kommissionierer die Lagerzone verlassen, seinen Auftrag selbst verpacken oder zu einer Weiterbearbeitung abgeben.
Fazit
Der systemseitige Abschluss wird unterschiedlich realisiert. Je nach eingesetztem Kommissionierverfahren wird der Kommissionierer informiert und klar aufgefordert, die weiteren Schritte durchzuführen. Die genaue Zeit wird dabei erfasst.
Kommissionierung im Lager gehört in einem Logistik- oder Produktions-Unternehmen zu den wichtigsten Tätigkeiten. Die Qualität, die Fehlerquote, die Kommissionierleistung und die Zusammenführung der Teilmengen sind bei beleglosen Kommissioniersystemen deutlich besser.
Das Lagerverwaltungssystem kann jeden Kundenauftrag in dem Kommissioniervorgang exakt nachverfolgen. Mehrere Datenerfassungsgeräte und Systeme stehen für die elektronische Datenerfassung zur Verfügung. Sprechen Sie mit uns. Wir helfen Ihnen gerne, Ihre Kommissionierung optimal zu gestalten.
Haben Sie noch weitere Fragen zu Ihrer Kommissionierung?
Sprechen Sie direkt mit unseren Experten. Wir helfen Ihnen gerne.